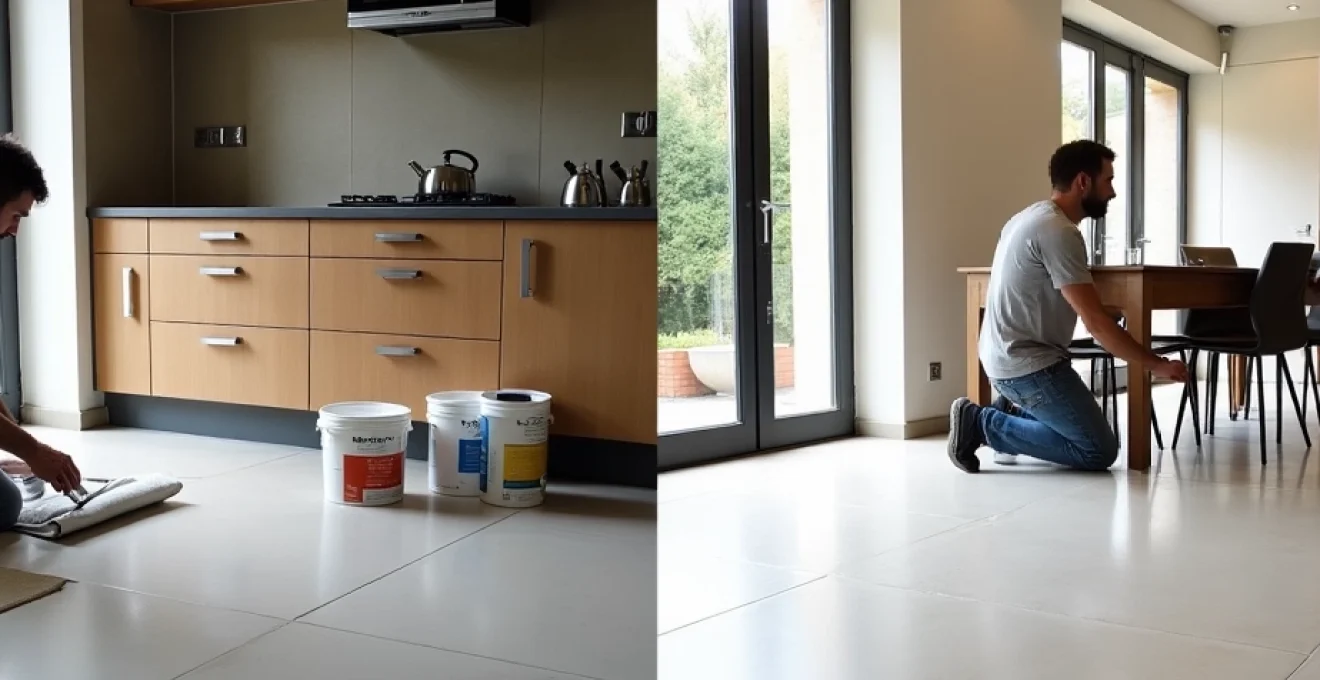
Le béton ciré s’impose aujourd’hui comme une solution de rénovation élégante pour transformer un sol carrelé sans travaux de démolition conséquents. Cette technique, qui consiste à appliquer une fine couche de béton décoratif sur un carrelage existant, permet de moderniser un intérieur tout en conservant le support d’origine. Avec son aspect contemporain, sa surface continue sans joints et ses nombreuses possibilités de teintes, le béton ciré offre une alternative esthétique et pratique aux revêtements traditionnels. Cette méthode de recouvrement présente l’avantage considérable d’éviter les désagréments liés à la dépose d’un carrelage : poussière, gravats, et modification des niveaux de sol.
L’application d’un béton ciré sur carrelage au sol représente une solution particulièrement adaptée aux projets de rénovation où le gain de temps et la limitation des nuisances constituent des priorités. Avec une épaisseur généralement comprise entre 3 et 5 millimètres, ce revêtement permet de conserver les huisseries existantes sans nécessiter de modifications. La diversité des formulations disponibles sur le marché et l’évolution des techniques d’application ont considérablement démocratisé cette solution, autrefois réservée aux professionnels du bâtiment.
Compatibilité du béton ciré avec différents types de carrelage
La réussite d’un projet de recouvrement par béton ciré dépend en grande partie de la nature du support existant. Tous les types de carrelage ne présentent pas les mêmes caractéristiques d’adhérence et certains nécessiteront des préparations spécifiques. Dans tous les cas, il est essentiel de s’assurer que le carrelage existant est sain, solidement fixé au sol et ne présente pas de désordres structurels importants, comme des fissures traversantes ou des carreaux descellés.
Application sur carrelage céramique : spécificités techniques
Le carrelage céramique traditionnel constitue généralement un excellent support pour l’application d’un béton ciré. Sa surface vitrifiée nécessite cependant l’emploi d’un primaire d’accrochage spécifique pour assurer une adhérence optimale du revêtement. La préparation consiste d’abord à dégraisser soigneusement la surface pour éliminer toute trace de cire ou de produit d’entretien qui pourrait compromettre l’adhérence. Un ponçage léger de la surface du carrelage céramique est souvent recommandé pour créer une légère rugosité favorable à l’accroche.
La principale difficulté technique réside dans le traitement des joints, généralement en creux par rapport à la surface des carreaux. Ces dépressions devront être comblées lors de la phase de préparation pour éviter que le dessin du carrelage ne réapparaisse avec le temps sur la surface du béton ciré. L’utilisation d’un ragréage fibré ou d’un mortier de réparation spécifique est généralement préconisée pour cette opération.
Béton ciré sur carreaux de grès cérame : adhérence et préparation
Le grès cérame, par sa très faible porosité et sa dureté exceptionnelle, représente un défi particulier pour l’application d’un béton ciré. Sa surface particulièrement lisse et compacte nécessite un traitement préparatoire rigoureux pour garantir une adhérence durable du revêtement. Un ponçage mécanique avec des disques diamantés est souvent nécessaire pour créer une microrugosité favorable à l’accroche du primaire.
L’utilisation d’un primaire d’accrochage haute performance, spécifiquement formulé pour les surfaces non poreuses, est absolument indispensable dans ce cas de figure. Les primaires à base de résines époxy bi-composantes offrent généralement les meilleures performances sur ce type de support. La préparation des joints requiert également une attention particulière, les joints du grès cérame étant souvent plus fins et moins profonds que ceux des carrelages traditionnels.
Recouvrement de faïence murale : adaptations nécessaires
Bien que notre sujet principal concerne les sols, il est intéressant de noter que le béton ciré peut également recouvrir des surfaces murales carrelées comme les faïences. Cette application verticale nécessite toutefois des adaptations spécifiques dans la formulation du produit. Pour éviter les coulures et faciliter l’application, des bétons cirés thixotropes, c’est-à-dire dont la viscosité augmente au repos, sont privilégiés.
La préparation de la faïence murale suit globalement les mêmes principes que pour un carrelage au sol : nettoyage, dégraissage et application d’un primaire d’accrochage. Cependant, l’aspect vertical de l’application impose des contraintes supplémentaires, notamment en termes d’épaisseur de couche appliquée. Des passes plus fines et plus nombreuses sont généralement préférables pour éviter les problèmes de fluage ou d’arrachement du produit.
Traitement des carrelages antidérapants et texturés
Les carrelages antidérapants ou présentant un relief prononcé constituent un cas particulier qui nécessite une préparation approfondie. Leur texture rugueuse, conçue pour améliorer l’adhérence en milieu humide, représente un obstacle à l’obtention d’une surface plane et lisse en béton ciré. Un ragréage préalable plus conséquent sera nécessaire pour combler les aspérités et créer une surface uniforme.
Dans certains cas extrêmes où le relief est particulièrement prononcé, l’application d’une résine autolissante ou d’un mortier de nivellement peut s’avérer nécessaire avant même l’application du primaire d’accrochage. Cette étape supplémentaire permet de créer une surface intermédiaire parfaitement plane qui servira de support au béton ciré. Le temps de séchage de cette couche de préparation doit être scrupuleusement respecté selon les préconisations du fabricant.
Les carrelages très texturés ou fortement antidérapants peuvent nécessiter jusqu’à trois couches préparatoires successives pour obtenir une surface parfaitement uniforme avant l’application du béton ciré.
Préparation du support carrelé avant application
La qualité de la préparation du support conditionne directement la durabilité et l’aspect final du béton ciré. Cette phase préliminaire, souvent négligée par les applicateurs amateurs, représente pourtant plus de 50% du travail et garantit l’adhérence à long terme du revêtement. Une préparation minutieuse permettra également d’éviter certains désordres esthétiques, comme la réapparition du dessin du carrelage (effet « fantôme ») au travers du béton ciré.
Diagnostic et nettoyage approfondi des joints et carreaux
Avant toute intervention, un diagnostic complet de l’état du carrelage existant s’impose. Cette inspection permet d’identifier les carreaux descellés ou fissurés qui devront être remplacés ou consolidés avant l’application du béton ciré. Un test sonore, réalisé en tapotant légèrement la surface avec un objet métallique, permet de repérer les zones mal adhérentes qui sonneront « creux ».
Le nettoyage du carrelage représente ensuite une étape fondamentale. Il s’effectue généralement en deux temps : d’abord un dégraissage profond avec un détergent alcalin puissant pour éliminer les résidus de cire, de produits d’entretien et de graisses, puis un rinçage abondant à l’eau claire. Pour les joints particulièrement encrassés, un nettoyage spécifique à la brosse avec un produit détartrant peut s’avérer nécessaire. La surface doit être parfaitement sèche avant de poursuivre le processus.
Primaires d’accrochage spécifiques : weber prim AD vs mapei eco prim grip
Le choix du primaire d’accrochage est déterminant pour assurer la liaison entre le carrelage existant et le béton ciré. Deux produits professionnels se distinguent particulièrement pour cette application : le Weber Prim AD et le Mapei Eco Prim Grip. Ces primaires spécifiques créent une surface rugueuse qui favorise l’adhérence mécanique des couches suivantes.
Le Weber Prim AD se caractérise par sa formulation à base de résines synthétiques en dispersion aqueuse, offrant une adhérence remarquable sur supports fermés comme le carrelage. Son temps de séchage relativement court (environ 2 heures) permet d’enchaîner rapidement les opérations. Le Mapei Eco Prim Grip, quant à lui, présente l’avantage d’être prêt à l’emploi et d’offrir un temps ouvert plus long, ce qui facilite son application sur de grandes surfaces. Sa couleur rosée permet également de visualiser facilement les zones traitées.
Ces primaires s’appliquent généralement au rouleau, en une couche fine et régulière, en prenant soin de bien pénétrer dans les joints. Un temps de séchage complet, selon les préconisations du fabricant, doit être respecté avant l’application des couches suivantes. Il est essentiel de ne pas surdoser le primaire pour éviter la formation d’un film trop épais qui pourrait nuire à l’adhérence finale.
Traitement des défauts et fissures avec résines époxy
Les fissures, éclats ou autres défauts ponctuels du carrelage doivent faire l’objet d’un traitement spécifique avant l’application du béton ciré. Pour les fissures importantes ou les joints de carrelage particulièrement dégradés, l’utilisation de résines époxy permet d’obtenir une réparation durable et parfaitement solidaire du support.
Ces résines bi-composantes, mélangées selon les proportions indiquées par le fabricant, sont injectées dans les fissures à l’aide d’une seringue ou d’un pistolet adapté. Pour les fissures larges, l’ajout de charges minérales (silice fine) à la résine permet d’obtenir un mortier époxy qui comblera efficacement les vides. Un temps de polymérisation complet, généralement de 24 heures, doit être respecté avant de poursuivre les travaux.
Pour les défauts plus superficiels comme les éclats ou les épaufrures, un mortier de réparation à prise rapide peut être suffisant. Dans tous les cas, la surface réparée doit être parfaitement affleurante avec le reste du carrelage pour éviter la formation de ressauts qui se répercuteraient dans le béton ciré.
Pontage et ragréage des joints de carrelage
Le traitement des joints de carrelage constitue l’une des étapes les plus importantes de la préparation. Sans un comblement efficace, le dessin du carrelage risque de réapparaître à terme sur la surface du béton ciré, un phénomène connu sous le nom de « télégraphing ». Deux approches principales existent pour prévenir ce problème.
La première consiste à appliquer un mortier de ragréage fibré sur l’ensemble de la surface, en veillant à bien combler tous les joints. Ce ragréage, d’une épaisseur de 3 à 5 mm selon la profondeur des joints, crée une surface continue qui servira de support au béton ciré. Pour les joints particulièrement profonds, il peut être nécessaire d’appliquer une couche préalable de mortier de jointoiement pour éviter une consommation excessive de ragréage.
La seconde approche, plus précise mais aussi plus laborieuse, consiste à traiter individuellement chaque joint avec un mortier de réparation à prise rapide. Cette méthode permet d’économiser du matériau mais nécessite un temps d’application plus long. Elle est généralement réservée aux surfaces restreintes ou aux travaux minutieux.
Mise en place d’un treillis de fibre de verre : technique et intérêt
Pour renforcer la résistance mécanique du système et prévenir d’éventuelles fissurations, l’incorporation d’un treillis en fibre de verre dans les couches préparatoires présente un intérêt certain. Ce treillis, d’une maille généralement comprise entre 4×4 mm et 10×10 mm, apporte une cohésion supplémentaire à l’ensemble du revêtement et limite les risques de fissuration liés aux mouvements différentiels entre le support carrelé et le béton ciré.
La mise en œuvre de ce renforcement s’effectue généralement lors de l’application du ragréage. Après avoir appliqué une première couche de mortier, le treillis est déroulé sur la surface encore fraîche, puis recouvert d’une seconde passe de produit. Les lés de treillis doivent se chevaucher sur 5 à 10 cm pour assurer la continuité du renforcement. Cette armature est particulièrement recommandée dans les zones à fort passage ou lorsque le carrelage existant présente des signes de faiblesse.
Pour les surfaces importantes ou lorsque les mouvements du support sont prévisibles (comme dans le cas d’un plancher bois recouvert de carrelage), l’utilisation d’un treillis devient pratiquement incontournable pour garantir la pérennité du béton ciré. Le coût supplémentaire et le temps d’application additionnel sont largement compensés par la durabilité accrue du revêtement final.
Techniques d’application du béton ciré sur sol carrelé
Une fois la phase de préparation achevée, l’application proprement dite du béton ciré peut commencer. Plusieurs méthodes existent, chacune présentant ses avantages et ses contraintes spécifiques. Le choix de la technique dépendra de la nature du support, de la surface à traiter, de l’effet esthétique recherché et, bien sûr, du niveau de compétence de l’applicateur.
Méthode en couches minces pour surfaces résidentielles
La technique en couches minces constitue l’approche la plus répandue pour les applications résidentielles. Elle consiste à appliquer successivement 2 à 3 couches de béton ciré d’une épaisseur de 1 à 2 mm chacune. Cette méthode permet d’obtenir un contrôle précis de l’aspect final et facilite la gestion des nuances et effets décoratifs.
La première couche, souvent appelée « couche d’accroche » ou « scratch coat » en
anglais, constitue la base sur laquelle les couches de finition viendront se poser. Elle doit être appliquée avec soin, en veillant à bien couvrir l’intégralité de la surface et à pénétrer dans les moindres recoins. L’utilisation d’une taloche inox à bords arrondis permet d’obtenir une application uniforme sans marques disgracieuses. Cette première couche n’a pas vocation à créer un effet esthétique particulier, mais plutôt à établir une base solide et régulière.
Après un temps de séchage d’environ 24 heures, un ponçage léger est réalisé pour éliminer les défauts et aspérités. La deuxième couche, plus fine, peut alors être appliquée. C’est généralement lors de cette phase que l’applicateur travaille les effets décoratifs caractéristiques du béton ciré : mouvements de taloche circulaires, superpositions partielles ou effets de matière. Un nouveau ponçage, plus fin (grain 180 à 220), intervient après séchage pour préparer la surface à recevoir une éventuelle troisième couche ou directement les produits de finition.
Système bicouche avec finition cirée pour pièces humides
Pour les pièces humides comme les salles de bains ou les cuisines, un système bicouche avec finition cirée offre un excellent compromis entre esthétique et performances techniques. Cette méthode repose sur l’application d’une couche de base plus épaisse (2 à 3 mm) suivie d’une couche de finition enrichie en résines et en additifs hydrofuges. Ce système présente l’avantage d’une mise en œuvre plus rapide tout en garantissant une résistance accrue à l’humidité et aux taches.
La couche de base, généralement formulée avec un béton ciré à granulométrie moyenne (0,5 à 1 mm), est appliquée à la lisseuse ou à la taloche en mouvements amples et réguliers. Après séchage et ponçage (grain 120), la couche de finition, composée d’un béton ciré fin (granulométrie inférieure à 0,3 mm), est appliquée en fine épaisseur. Cette dernière couche concentre les agents hydrophobes et les résines qui conféreront au revêtement sa résistance à l’eau et aux agressions domestiques courantes.
La protection finale, réalisée à l’aide de cires spécifiques parfois mélangées à des résines polyuréthanes, vient compléter ce système en créant une barrière efficace contre l’infiltration d’eau tout en préservant l’aspect naturel du béton ciré. Ce type d’application convient particulièrement aux douches à l’italienne et aux plans vasques, zones particulièrement exposées aux projections d’eau.
Application monocouche de type mercadier EasyBéton
Pour les rénovateurs moins expérimentés ou les chantiers nécessitant une exécution rapide, les systèmes monocouche de type Mercadier EasyBéton représentent une alternative intéressante. Ces produits, spécifiquement formulés pour une application en couche unique, intègrent dans leur composition des adjuvants qui optimisent l’adhérence sur supports difficiles comme le carrelage. Ils permettent d’obtenir un résultat esthétique satisfaisant avec un temps d’application réduit.
L’application s’effectue en une seule passe d’une épaisseur de 2 à 3 mm à l’aide d’une lisseuse ou d’une taloche en inox. La consistance légèrement plus ferme de ces produits facilite leur maintien sur les surfaces verticales et permet de créer directement les effets décoratifs souhaités. Un ponçage après séchage complet (24 à 48 heures selon les conditions ambiantes) permet d’obtenir la finesse de grain désirée avant l’application des produits de protection.
Si cette méthode présente l’avantage indéniable de la rapidité, elle offre néanmoins moins de possibilités en termes d’effets décoratifs et de nuances que les systèmes multicouches. Elle convient parfaitement aux petites surfaces ou aux projets où le facteur temps constitue une contrainte majeure.
Talochage manuel vs projection mécanique
Le talochage manuel représente la méthode traditionnelle d’application du béton ciré. Cette technique, qui fait appel au savoir-faire et à la sensibilité de l’artisan, permet d’obtenir des effets personnalisés et une finition parfaitement maîtrisée. Les mouvements de la taloche, leur pression, leur amplitude et leur direction influencent directement l’aspect final du revêtement. Cette approche artisanale confère à chaque réalisation un caractère unique qui constitue l’un des atouts majeurs du béton ciré.
La projection mécanique, moins courante pour les applications résidentielles, offre quant à elle une productivité nettement supérieure, particulièrement adaptée aux grandes surfaces. Elle s’effectue à l’aide d’une machine spécifique qui projette le béton ciré sur le support avant un lissage à la taloche mécanique ou manuelle. Si cette méthode permet de traiter rapidement des surfaces importantes, elle offre un contrôle moins précis des effets décoratifs et nécessite un équipement spécialisé rarement accessible aux particuliers.
Le choix entre talochage manuel et projection mécanique doit tenir compte non seulement de la surface à traiter, mais également du niveau de personnalisation souhaité et du budget disponible pour la main-d’œuvre, généralement plus importante dans le cas d’une application manuelle soignée.
Formulations spécifiques pour recouvrement de carrelage
Le marché propose aujourd’hui des formulations de béton ciré spécifiquement conçues pour l’application sur carrelage. Ces produits intègrent des résines et des adjuvants qui optimisent l’adhérence sur supports difficiles et réduisent les risques de fissuration liés aux mouvements différentiels entre le support et le revêtement. Les fabricants ont développé des systèmes complets comprenant primaires, mortiers de base, couches de finition et produits de protection parfaitement compatibles entre eux.
Les bétons cirés dernière génération enrichis en polymères offrent une flexibilité accrue qui leur permet de s’adapter aux légers mouvements du support sans se fissurer. Leur formulation intègre généralement des fibres synthétiques microscopiques qui renforcent la cohésion du matériau et limitent les risques de microfissuration. Ces produits présentent également une résistance supérieure à l’abrasion et aux chocs, caractéristiques particulièrement appréciables pour une application au sol.
Certains fabricants proposent des bétons cirés bi-composants, associant une partie poudre (ciment, charges minérales et additifs) à un liquide à base de résines acryliques ou époxydiques. Ces systèmes, bien que plus complexes à mettre en œuvre, offrent généralement des performances mécaniques supérieures aux produits mono-composants. Leur résistance à l’usure et leur stabilité dans le temps en font des solutions particulièrement adaptées aux zones à fort passage comme les entrées ou les couloirs.
Pour les pièces humides, des formulations spécifiques intégrant des hydrofuges de masse permettent d’obtenir un béton ciré naturellement résistant à l’eau, même avant l’application des produits de protection de surface. Ces produits, généralement formulés avec des résines polyuréthanes en émulsion aqueuse, offrent une sécurité supplémentaire en cas de défaut ponctuel du traitement de surface.
Traitements de finition et protection du béton ciré au sol
La protection du béton ciré constitue une étape cruciale qui conditionne directement la durabilité du revêtement et sa résistance aux taches et à l’usure. Le béton ciré brut, poreux par nature, nécessite l’application de produits de finition qui formeront une barrière protectrice tout en préservant ses qualités esthétiques. Le choix du traitement dépendra de l’exposition du sol aux sollicitations mécaniques, à l’humidité et aux agents tachants.
Vernis polyuréthanes bi-composants pour zones à fort passage
Pour les zones à fort passage comme les couloirs, entrées ou pièces à vivre, les vernis polyuréthanes bi-composants constituent la solution la plus performante. Ces produits, issus des technologies industrielles, forment un film protecteur particulièrement résistant à l’abrasion, aux rayures et aux taches. Leur application s’effectue généralement en deux couches croisées à l’aide d’un rouleau à poils courts spécial « phase solvant » ou d’un spalter selon la viscosité du produit.
Ces vernis existent en différentes finitions (mate, satinée ou brillante) qui influenceront non seulement l’aspect esthétique du sol, mais également sa résistance à l’encrassement. Les finitions satinées ou brillantes, bien que plus marquées visuellement, offrent généralement une meilleure résistance aux taches et facilitent l’entretien quotidien. Les versions mates, plus discrètes et plus proches de l’aspect naturel du béton, nécessiteront un entretien plus régulier.
Malgré leurs excellentes performances, ces vernis présentent quelques inconvénients : leur application requiert un savoir-faire technique pour éviter les reprises et traces de rouleau, et les versions solvantées dégagent des odeurs fortes qui imposent une ventilation efficace pendant et après l’application. Des alternatives en phase aqueuse, bien que légèrement moins performantes, offrent aujourd’hui un compromis intéressant pour les applications résidentielles.
Cires naturelles : application et entretien selon marius aurenti
Pour ceux qui privilégient un aspect plus naturel et une démarche écologique, les cires naturelles constituent une alternative séduisante aux vernis synthétiques. Marius Aurenti, référence dans le domaine du béton ciré haut de gamme, propose une approche basée sur l’utilisation de cires naturelles d’origine végétale ou minérale qui nourrissent le béton en profondeur tout en formant une protection de surface.
L’application de ces cires s’effectue généralement en trois étapes : d’abord un bouche-pores qui pénètre dans la structure du béton pour limiter son absorption, puis deux couches de cire proprement dite, appliquées à 24 heures d’intervalle. La mise en œuvre se fait à l’aide d’un applicateur spécifique (spalter, chiffon non pelucheux ou monobrosse selon les surfaces) en mouvements circulaires réguliers. Un lustrage final à la monobrosse équipée d’un pad doux ou au chiffon permet d’obtenir un aspect satiné particulièrement élégant.
Si cette solution offre un rendu esthétique incomparable qui met en valeur la minéralité du béton ciré, elle nécessite un entretien plus régulier que les vernis polyuréthanes. Marius Aurenti recommande l’application d’une couche d’entretien tous les 6 à 12 mois selon l’intensité d’utilisation du sol. Ce geste d’entretien, relativement simple à réaliser, permet de régénérer la protection et de maintenir l’aspect esthétique du revêtement sur le long terme.
Hydrofuges et oléofuges spécifiques pour cuisines et salles de bain
Les pièces d’eau comme les cuisines et salles de bains constituent des environnements particulièrement exigeants qui nécessitent des traitements spécifiques. Les hydrofuges et oléofuges professionnels offrent une protection renforcée contre l’eau et les corps gras, principales sources de dégradation dans ces espaces. Ces produits, généralement à base de résines fluorées ou siloxanes, pénètrent dans la structure du béton ciré pour former une barrière imperméable tout en laissant le matériau respirer.
Contrairement aux vernis filmogènes, ces traitements ne modifient pas l’aspect de surface du béton ciré et préservent sa texture naturelle. Ils s’appliquent généralement en deux couches « mouillé sur mouillé » à l’aide d’un pulvérisateur basse pression ou d’un rouleau, en veillant à bien saturer le support. Pour une efficacité optimale, certains fabricants recommandent d’associer un hydrofuge de profondeur à un traitement de surface plus spécifiquement orienté contre les taches d’origine grasse.
Dans les zones directement exposées aux projections d’eau comme les douches à l’italienne, un traitement renforcé peut s’avérer nécessaire. Certains systèmes professionnels proposent des solutions complètes associant un primaire d’imprégnation, un hydrofuge de masse et un traitement de surface, garantissant une imperméabilité totale même en cas d’exposition prolongée à l’eau. Ces traitements sophistiqués, bien que plus coûteux, offrent une sécurité maximale dans les zones critiques.
Protection anti-UV pour béton ciré en extérieur sur terrasse carrelée
L’application d’un béton ciré sur une terrasse carrelée extérieure nécessite une protection spécifique contre les rayonnements ultraviolets, principal facteur de dégradation des résines en extérieur. Les vernis polyuréthanes aliphatiques, contrairement à leurs homologues aromatiques utilisés en intérieur, offrent une résistance exceptionnelle au jaunissement et à la dégradation sous l’effet des UV.
Ces vernis haute performance, initialement développés pour l’industrie nautique ou aéronautique, forment une protection durable qui conserve sa transparence et ses propriétés mécaniques même après une exposition prolongée au soleil. Leur application s’effectue généralement en trois couches fines à 24 heures d’intervalle, la dernière pouvant être additionnée de charges antidérapantes pour sécuriser les zones potentiellement glissantes en présence d’eau.
Pour les bétons cirés de couleur claire, l’ajout d’absorbeurs d’UV dans la formulation du vernis permet de prévenir le jaunissement progressif du support. Cette précaution est particulièrement importante pour les terrasses situées en altitude ou dans les régions méridionales, où l’intensité du rayonnement UV est plus importante. Ces additifs, bien que légèrement plus coûteux, contribuent significativement à la pérennité esthétique du revêtement extérieur.